Improving warehouse efficiency requires a strategic approach that combines layout optimization, technology adoption, and process refinement. Below are actionable strategies to maximize productivity and reduce operational costs:
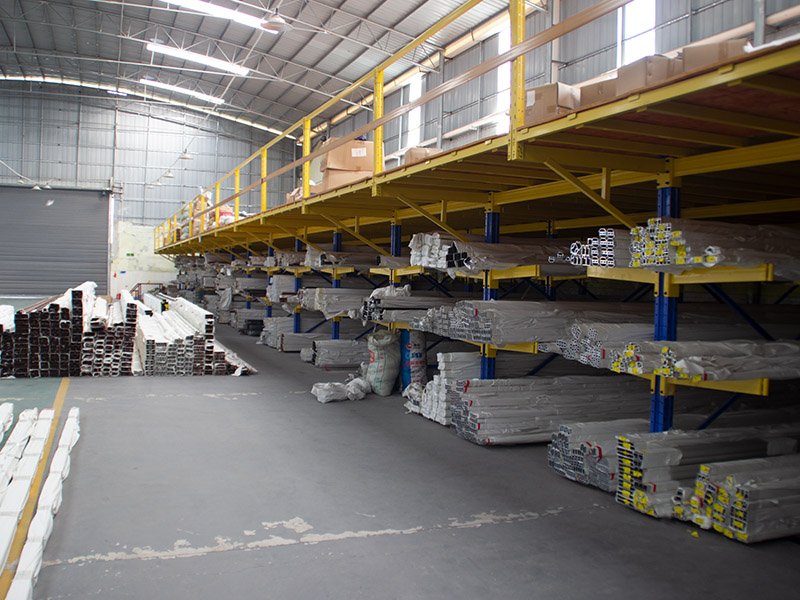
1. Optimize Warehouse Layout
- Zoning and Flow Design: Divide the warehouse into functional zones (e.g., receiving, storage, picking, shipping) to streamline workflows.
- Vertical Space Utilization: Install high-density shelving (e.g., pallet racks, cantilever racks) or mezzanine systems to maximize vertical storage.
- Aisle Width Adjustment: Balance aisle width with equipment needs (e.g., narrow aisles for forklifts or automated guided vehicles (AGVs)).
2. Implement Advanced Storage Systems
- Automated Solutions: Deploy automated storage and retrieval systems (AS/RS), shuttle racks, or conveyor belts to reduce manual labor and speed up operations.
- Smart Shelving: Use adjustable or modular racks to accommodate diverse product sizes and seasonal demand changes.
3. Leverage Technology
- Warehouse Management Systems (WMS): Integrate WMS software for real-time inventory tracking, order prioritization, and data-driven decision-making.
- IoT and RFID: Employ IoT sensors and RFID tags to monitor inventory levels, track goods, and prevent stockouts or overstocking.
- Barcode Scanning: Accelerate picking and reduce errors with barcode scanners linked to your WMS.
4. Improve Inventory Management
- ABC Analysis: Prioritize high-value, fast-moving items (Category A) for easy access, while storing slower-moving goods (Categories B/C) in less accessible areas.
- Just-in-Time (JIT): Align inventory with demand to minimize excess stock and storage costs.
- Cycle Counting: Conduct regular partial inventory checks instead of full shutdowns for audits.
5. Enhance Picking and Packing Processes
- Batch Picking: Group similar orders to reduce travel time.
- Zone Picking: Assign workers to specific zones to specialize in certain tasks.
- Automated Packaging: Use machines for sealing, labeling, and sorting to accelerate order fulfillment.
6. Train and Empower Staff
- Cross-Training: Equip employees with skills to handle multiple roles, ensuring flexibility during peak periods.
- Ergonomic Tools: Provide equipment like lift-assist devices to reduce fatigue and injuries.
- Performance Incentives: Reward teams for meeting efficiency targets (e.g., faster picking rates).
7. Adopt Lean Principles
- 5S Methodology:
- Sort: Remove unnecessary items.
- Set in Order: Organize tools and inventory logically.
- Shine: Maintain cleanliness.
- Standardize: Create consistent workflows.
- Sustain: Regularly review and improve processes.
- Kaizen (Continuous Improvement): Encourage small, incremental changes to eliminate waste.
8. Monitor and Analyze Performance
- KPIs: Track metrics like order accuracy, picking speed, inventory turnover, and space utilization.
- Data Analytics: Use dashboards to identify bottlenecks and optimize resource allocation.
9. Energy and Cost Efficiency
- LED Lighting: Reduce energy consumption with motion-sensor lighting.
- Climate Control: Optimize HVAC systems in temperature-sensitive warehouses to cut energy costs.
10. Regular Maintenance
- Equipment Checks: Schedule routine inspections for forklifts, conveyors, and shelving to prevent downtime.
- Update Infrastructure: Replace outdated racks or tools with modern, durable alternatives.
By integrating these strategies, businesses can achieve faster order fulfillment, lower operational costs, and improved scalability. Tailor solutions to your warehouse’s specific needs, and prioritize technologies that align with long-term growth goals.